Understanding Injection Molding Tooling: A Comprehensive Guide
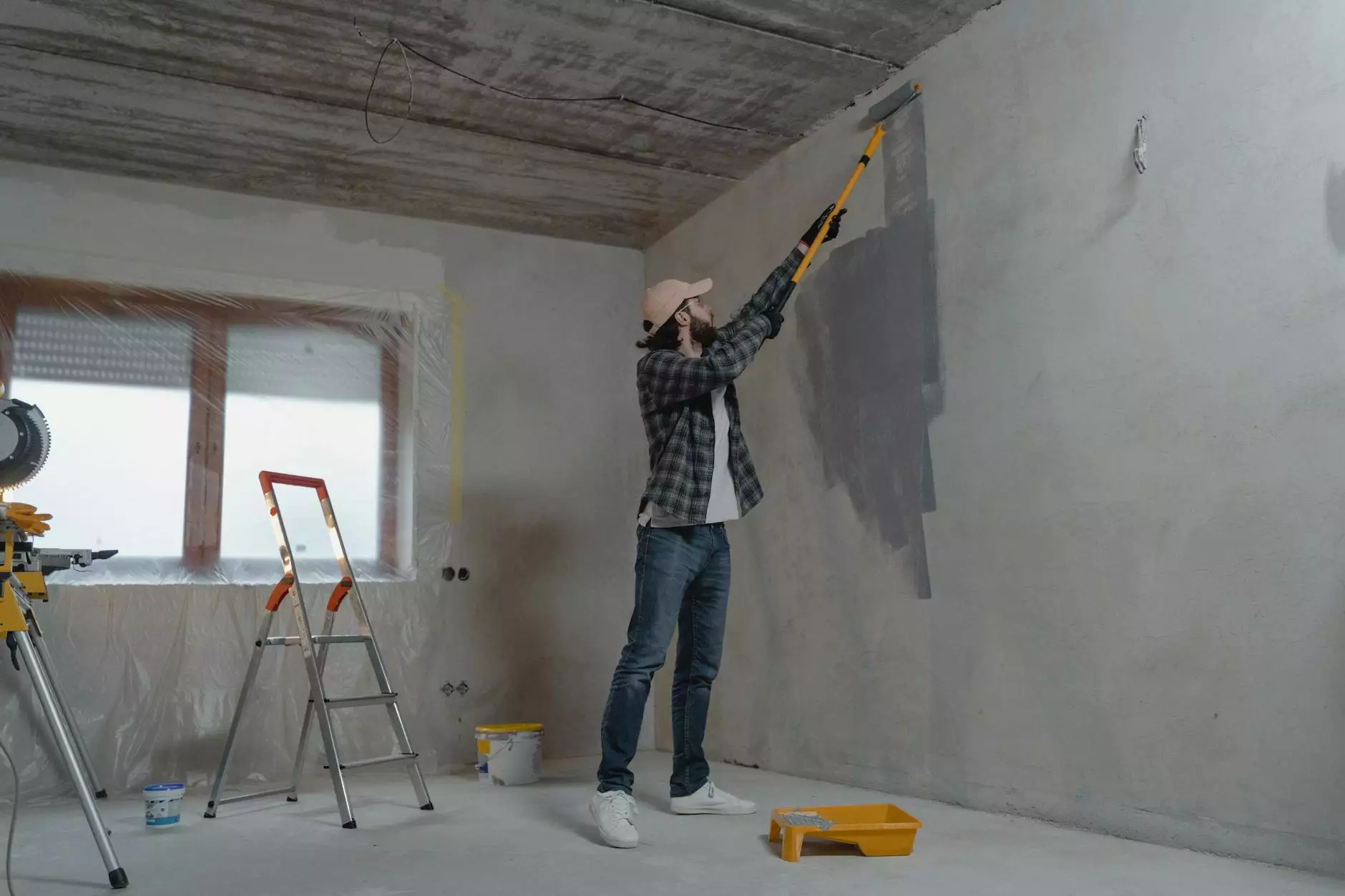
Introduction to Injection Molding Tooling
Injection molding tooling is a crucial process in the manufacturing industry, especially for companies involved in metal fabrication. This technique is used to create complex shapes and components with high precision through the injection of molten material into a mold. In this article, we will delve into the details of injection molding tooling, exploring its processes, advantages, and applications in various industries.
What is Injection Molding Tooling?
At its core, injection molding tooling refers to the molds and associated tooling used to manufacture parts by injecting molten material, typically thermoplastics, into a mold cavity. The process allows for:
- High-volume production of parts
- Consistency in part dimensions
- Minimized waste due to efficient material usage
- Ability to mold complex shapes and intricacies
The injection molding process is indispensable in creating parts for various industries, including automotive, consumer goods, medical devices, and electronics.
The Injection Molding Process Explained
1. Design and Prototyping
The injection molding process begins with the design phase. Engineers create a 3D model of the part to be manufactured. This model is essential in defining the specifications and requirements needed for the mold design.
2. Mold Creation
The next step involves creating the actual mold. The molds are typically made from high-quality steel or aluminum and are designed to withstand the high pressures of the injection molding process. Several factors must be considered in mold design, including:
- Part complexity and geometry
- Material flow characteristics
- Cooling systems for temperature control
- Mold maintenance and serviceability
3. Injection Phase
During this phase, the chosen material is heated until it becomes molten and is injected into the mold cavity under high pressure. The injection unit must precisely control the temperature and duration of injection to achieve optimal results.
4. Cooling and Ejection
Once the mold is filled, the material cools and solidifies. This cooling phase is critical in determining the overall quality and dimensional accuracy of the final product. After adequate cooling, the mold opens, and ejector pins release the finished part.
Benefits of Injection Molding Tooling
The use of injection molding tooling comes with numerous benefits that make it a preferred method for manufacturers, including:
- Cost-Effectiveness: While the initial cost of mold creation may be high, the low cost per part in high-volume production makes it economical in the long run.
- Speed and Efficiency: Injection molding allows for rapid production cycles, enabling manufacturers to meet high demand quickly.
- Versatility: This process can accommodate a wide range of materials and can produce diverse parts, from simple designs to very intricate shapes.
- High Precision: Injection molding tooling achieves extremely tight tolerances, producing parts that require minimal post-processing.
These advantages make injection molding tooling a preferred choice in various sectors, such as automotive, medical, and consumer products.
Applications of Injection Molding Tooling
The applications of injection molding tooling extend across multiple industries:
- Automotive: Used in manufacturing components such as dashboard parts, housings, and exterior trims.
- Consumer Electronics: Essential for components found in phones, chargers, and other electronic devices.
- Medical Devices: Utilized for creating precision components for surgical tools, diagnostic equipment, and pharmaceutical packaging.
- Toys and Consumer Goods: Enables the production of colorful and intricate designs that meet consumer demand.
The broad range of applications highlights the versatility and critical role of injection molding tooling in modern manufacturing.
Challenges in Injection Molding Tooling
Despite its numerous benefits, there are challenges associated with injection molding tooling, including:
- Mold Design Complexity: Designing a mold that can produce high-quality parts while also being maintainable and cost-effective can be a challenge.
- High Initial Investment: The cost of creating molds can be significant, which may pose challenges for smaller companies.
- Material Limitations: Not all materials are suitable for injection molding. The choice of material greatly influences the final product's properties.
Addressing these challenges requires expertise and the use of advanced technology in mold design and manufacturing.
The Future of Injection Molding Tooling
The future of injection molding tooling looks promising with advances in technology. Innovations are shaping the way manufacturers approach mold design and production:
- 3D Printing Integration: 3D printing technology is increasingly being integrated into mold manufacturing, allowing for rapid prototyping and more complex designs.
- Smart Manufacturing: The use of IoT and AI in injection molding processes can enhance production efficiency and quality control.
- Sustainable Practices: As industries shift towards sustainability, the development of biodegradable materials and recycling techniques is becoming critical.
These advancements are set to enhance the efficiency, sustainability, and effectiveness of injection molding tooling in the years to come.
Conclusion
In summary, injection molding tooling is an essential technology in the metal fabrication industry, providing manufacturers with the capability to produce high-quality, precision parts efficiently. As technology continues to evolve, the potential for innovation in injection molding tooling will only expand, offering new opportunities for businesses like Deep Mould to thrive in a competitive market. By understanding the intricacies and advantages of this process, companies can make informed decisions to leverage injection molding tooling for their manufacturing needs.