The Ultimate Guide to Plastic Mold Tooling: Innovations and Best Practices
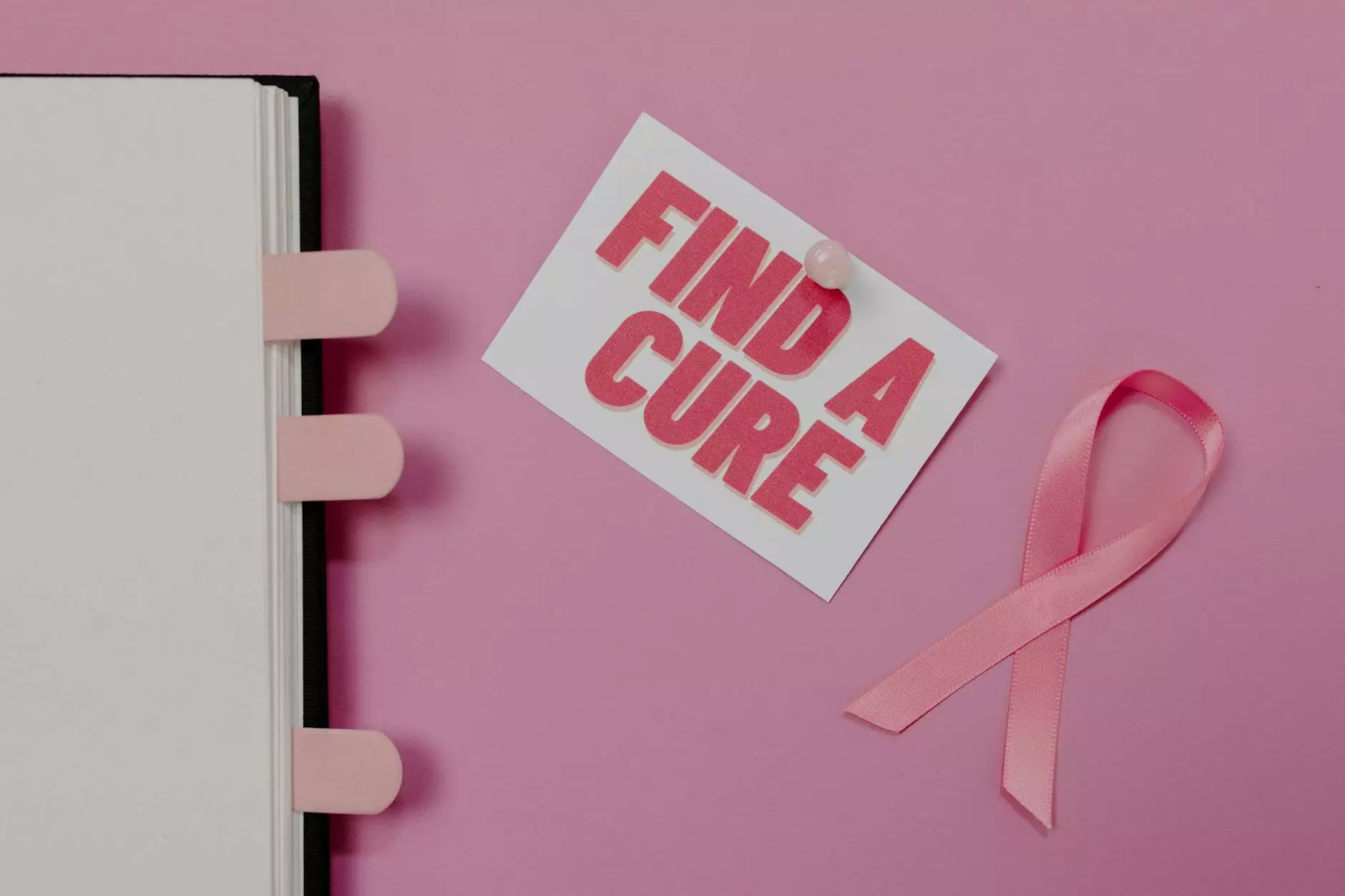
In today's competitive manufacturing landscape, mastering plastic mold tooling is crucial for businesses aiming to enhance efficiency and product quality. This comprehensive guide delves deep into the world of plastic mold tooling, exploring its importance, techniques, innovations, and how companies—especially those in metal fabrication—can leverage these tools for success.
Understanding Plastic Mold Tooling
Plastic mold tooling refers to the process of designing and manufacturing molds that are used to shape and form plastic products. This vital step in the manufacturing cycle plays a significant role in determining the quality, precision, and durability of the final product. The process involves several stages, each crucial for ensuring that the final molded product meets the required specifications.
Importance of Plastic Mold Tooling
The significance of plastic mold tooling cannot be overstated. Here are a few key reasons why it is essential in the manufacturing process:
- Cost Efficiency: Proper tooling reduces material waste and minimizes production costs.
- Precision and Quality: High-quality molds ensure that products have consistent dimensions and finish.
- Flexibility: Molds can be designed for various types of plastics, allowing for a diverse range of products.
- Time-Saving: Efficient mold design expedites the manufacturing process, leading to faster delivery times.
- Scalability: Once a mold is created, it can be used for mass production, making it easier to scale up operations.
Types of Plastic Mold Tooling
There are several types of plastic mold tooling, each designed for specific applications. Understanding these types can help businesses choose the right tools for their manufacturing needs.
1. Injection Molding
Injection molding is the most common type of plastic mold tooling. In this process, molten plastic is injected into a mold cavity, where it cools and solidifies into the desired shape. This method is ideal for producing large quantities of identical parts rapidly.
2. Blow Molding
Blow molding is used for hollow plastic parts such as bottles and containers. This process involves inflating hot plastic in a mold until it takes shape. It’s an effective method for creating seamless, hollow products.
3. Compression Molding
In compression molding, plastic is placed into an open mold, heated, and then pressed to shape. This method is commonly used for rubber and thermosetting plastics, producing high-strength parts.
4. Rotational Molding
Rotational molding involves rotating a mold filled with plastic resin around two axes. This technique forms hollow products like large containers and outdoor furniture with uniform wall thickness.
Key Components of Plastic Mold Tooling
Effective plastic mold tooling involves various components that work together to create the desired product. Here are the key elements:
- Mold Base: The foundation of the mold that holds all other components together.
- Mold Cavity: The area where plastic is injected to form the part.
- Cooling System: A network of channels that helps cool the molded product to reduce cycle times.
- Ejector System: Mechanisms that remove the finished part from the mold.
- Venting: Channels that allow air to escape from the mold during the injection process.
Innovations in Plastic Mold Tooling
The field of plastic mold tooling has seen remarkable innovations that enhance productivity and quality. Some of these advancements include:
1. 3D Printing Technology
3D printing has revolutionized mold design. Designers can create prototypes quickly and cost-effectively, allowing for rapid iteration and improvement. This technology makes it feasible to produce complex geometries that traditional methods cannot achieve.
2. Advanced Materials
The development of new materials for mold construction—such as high-strength aluminum and steel alloys—has improved mold durability and performance. These materials can withstand higher temperatures and pressures, leading to better production outcomes.
3. Automation and CNC Machining
Automation in the tooling process, particularly through the use of CNC (Computer Numerical Control) machines, has significantly increased precision and reduced human error. CNC machines can intricately carve molds with unmatched accuracy, paving the way for enhanced product quality.
4. Simulation Software
Advanced simulation software allows engineers to predict how materials behave during the mold filling process. This capability helps in optimizing the mold design, reducing cycle times, and minimizing defects in the final product.
Best Practices for Plastic Mold Tooling
To maximize the benefits of plastic mold tooling, businesses should adhere to several best practices:
1. Invest in Quality Design
Quality mold design is foundational. Engaging skilled designers and utilizing advanced software tools can lead to superior molds, which enhances product quality and reduces waste.
2. Regular Maintenance
Routine maintenance of molds is crucial to ensure longevity and reliability. Proper care can prevent costly downtime and enhance production efficiency. Scheduled inspections and cleaning should be part of your maintenance regimen.
3. Training and Development
Investing in employee training strengthens your workforce’s capabilities in operating and maintaining tooling equipment. Regular training ensures that your team is updated on the latest techniques and technologies in plastic mold tooling.
4. Collaborate with Experts
Partnering with experienced mold makers and engineers can provide invaluable insights. Their expertise can guide your tooling processes and help avoid common pitfalls in mold design and manufacturing.
Conclusion
Mastering plastic mold tooling is essential for any business in the metal fabrication sector that seeks to improve efficiency and product quality. By understanding the types of tooling, embracing innovations, and implementing best practices, companies can stay competitive in an ever-changing market. Remember, investing in quality tooling today paves the way for greater returns in the future. Explore how deepmould.net can assist you in your plastic mold tooling needs and elevate your manufacturing process.