The Ultimate Guide to Vacuum Stations: Enhancing Efficiency in Business
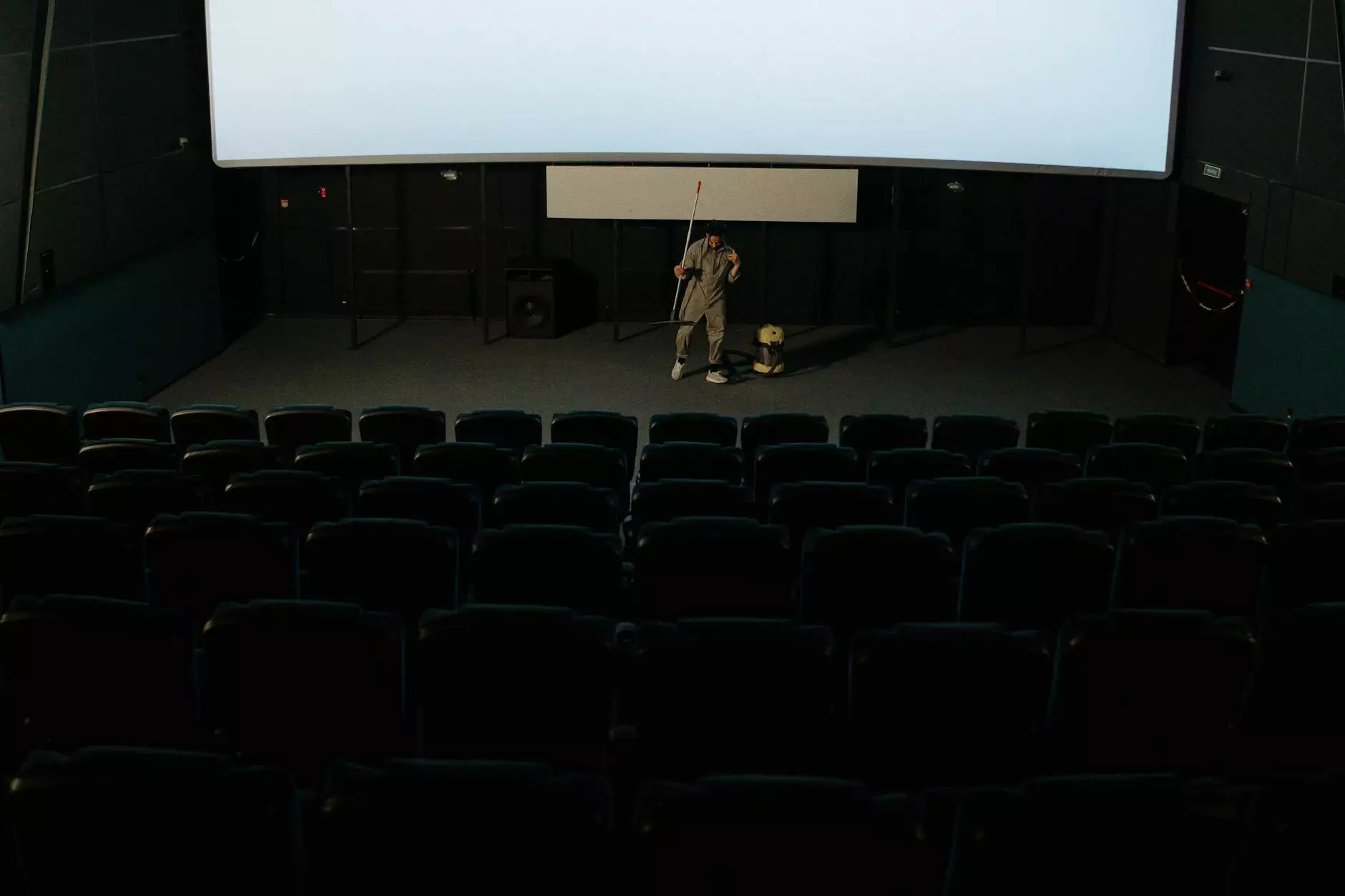
In today's highly competitive industrial landscape, maximizing efficiency is crucial for success. One of the key technologies that help businesses achieve this is the vacuum station. Used widely across various industries, vacuum stations are essential for a myriad of applications, ranging from food packaging to electronics manufacturing. In this comprehensive guide, we will delve into the nuances of vacuum stations, their functioning, components, and importance, particularly focusing on how businesses can benefit from their implementation.
What is a Vacuum Station?
A vacuum station is a system designed to create a controlled vacuum environment for various industrial processes. These stations utilize pumps and chambers to remove air and create a vacuum that is essential for the product integrity, safety, and performance in differing applications.
How Vacuum Stations Work
The efficiency of a vacuum station hinges on its ability to remove air or other gases from a specific area or system. The basic components of a vacuum station include:
- Vacuum Pump: This is the heart of the vacuum station, responsible for generating vacuum pressure by exhausting air from the system.
- Vacuum Chamber: This component provides a sealed space where the vacuum is maintained. Items are placed inside the chamber for processing.
- Valves: These control the flow of air and enable the sealing of the chamber to maintain the vacuum pressure.
- Hoses and Connectors: These facilitate the connection between the pump and the chamber, ensuring efficient air removal.
- Control System: A sophisticated control panel allows operators to monitor and adjust the performance of the vacuum station.
Applications of Vacuum Stations
Vacuum stations find usage in various industries due to their versatility and efficiency. Here are some of the primary applications:
- Food Packaging: Vacuum stations are vital in packaging perishable goods, enhancing shelf life by removing oxygen and sealing them tightly.
- Electronics Manufacturing: In the production of circuit boards and components, vacuum stations are utilized for soldering and removing contaminants.
- Medical Equipment: Sterilization processes often utilize vacuum stations to ensure that instruments are free from contaminants.
- Composites Manufacturing: Vacuum bagging processes allow for high-quality layering of materials without the introduction of air bubbles.
Types of Membranes Used in Vacuum Stations
Membranes play a crucial role in the functionality of vacuum stations, especially when it comes to sealing and maintaining vacuum pressure. Here are some common types:
Silicone Membranes
Silicone membranes are highly versatile and offer excellent temperature resistance, making them suitable for a range of applications. Their flexibility ensures a tight seal, which is critical in vacuum operations.
Rubber Membranes
Rubber membranes are favored for their durability and resistance to wear and tear. They are commonly used in sectors where a robust seal is required, such as in high-pressure applications.
Natural Rubber Membranes
Natural rubber membranes are often preferred for their eco-friendliness and excellent elasticity. They provide a reliable seal in various applications while being a sustainable choice.
Vacuum System Parts and Their Importance
Every component of a vacuum station plays a vital role in ensuring its productivity and efficiency. The parts must work harmoniously to maintain suitable vacuum levels and minimize downtime. Here are some essential components:
1. Vacuum Pump
The vacuum pump is crucial; without it, the operation of a vacuum station is impossible. Selecting the right type of pump, be it a rotary vane pump, diaphragm pump, or scroll pump, is essential depending on the required vacuum level and application.
2. Manifold System
A well-designed manifold system allows for multiple vacuum lines to be connected simultaneously. This is particularly beneficial in larger operations where several processes need to be vacuum sealed at once.
3. Filters
Incorporating filters within the vacuum system helps in capturing contaminants, thus prolonging the lifespan of the vacuum pump and preventing damage to other components.
4. Gauges
Accurate vacuum gauges are essential to provide real-time feedback on the vacuum levels. This information is crucial for operators to make necessary adjustments during the operation.
Benefits of Implementing Vacuum Stations in Your Business
Integrating a vacuum station into your business operations can yield various benefits, including:
- Enhanced Product Quality: By maintaining a vacuum environment, products can be packaged and processed without exposure to air, reducing oxidation and spoilage.
- Increased Shelf Life: Products sealed with vacuum technology tend to have a longer shelf life, which can significantly cut down on waste and improve profitability.
- Consistency and Efficiency: Automating vacuum processes leads to more consistent and efficient production lines, allowing for higher output with lower labor costs.
- Cost Savings: Decreasing product loss and improving processing times can lead to substantial cost savings for businesses.
Choosing the Right Vacuum Station for Your Business
When selecting a vacuum station for your business, consider the following factors:
1. Application Needs
Identify the specific processes where a vacuum station will be employed. Different applications may require various types of pumps and configurations.
2. Scale of Operations
For larger businesses, investing in a high-capacity vacuum station may be necessary. Assessing the volume of products and the required speed of operation is key.
3. Budget Considerations
As with any significant investment, budget constraints will influence your choice of vacuum station. Understand the total cost of ownership, including maintenance and operational costs.
Maintenance Best Practices for Vacuum Stations
Proper maintenance of your vacuum station is crucial to ensure longevity and efficiency. Here are best practices to follow:
- Regular Inspection: Routinely check all components for wear and tear, including hoses, valves, and seals.
- Routine Cleaning: Regularly clean the vacuum chamber and remove any debris or contaminants that may affect performance.
- Monitor Performance: Keep an eye on the gauges to ensure optimal performance and address any deviations promptly.
Future Trends in Vacuum Technology
The world of vacuum technology is continually evolving. Here are some trends to watch:
- Smart Technology Integration: The future of vacuum stations lies in smart technology, enabling remote monitoring and control for enhanced efficiency.
- Sustainability Focus: As industries push for greener solutions, vacuum technology is adapting to be more energy-efficient and utilize more sustainable materials.
- Advanced Materials: Innovations in materials science could lead to more durable and efficient membranes, increasing the versatility of vacuum stations.
Conclusion
In conclusion, utilizing a vacuum station can greatly enhance operational efficiencies across various industries. By understanding the components, applications, benefits, and maintenance of these systems, businesses can improve product quality, extend shelf life, and reduce costs. Investing in the right vacuum technology tailored to your specific needs is essential for staying competitive in today's market.
For more information on purchasing membranes, including silicone membranes, rubber membranes, natural rubber membranes, and various vacuum system parts, visit vacuum-presses.com. Empower your business today with the state-of-the-art vacuum solutions!